Three on the tree. Four on the Floor. The gear change mechanism is a component that is too often taken for granted but it is one of the more important features of the car. It must be quick and smooth in action, efficient and totally reliable. Modern driving conditions demand that the driver makes frequent gear changes and a mechanism that is temperamental or inaccurate can be both frustrating and dangerous as well as physically tiring.
Dog Clutches
Gear changes are no longer made by sliding the actual pinions in and out of mesh. The pinions on the modern gearbox are in constant-mesh. This means that the gears on the layshaft are an integral part of it, while those on the mainshaft are free to revolve without turning the shaft. Therefore, to bring a pair of gears into action, the mainshaft gear has to be locked to the shaft. This action will then provide a solid link between the layshaft and the mainshaft. Locking the gears to the mainshaft is effected by synchromesh-equipped dog clutch assemblies. The centre of the dog clutch is splined to the mainshaft and teeth at one end mesh with a matching set on the gear to be engaged. This gear is locked to the mainshaft through the dog clutch's splines.
The heart of the gear changing action is in the sliding of the dog clutches. To engage a gear the dog clutch must be slid up the mainshaft, to disengage it the dog clutch must be moved back down the shaft. Most dog clutches are in fact double-ended designs, which means that if they are moved in one direction they will engage one gear, if they are moved far enough in the other direction they will disengage from the first pinion and then engage a second. The advantage of this is that fewer dog clutches are needed. A typical four-speed gearbox will, for example, have three dog clutches, one for third and fourth gears, another for first and second and the third to engage reverse. There are three distinct parts to a gear change mechanism: the lever itself and its connections to the gearbox, the sliding forks that move the dog clutches in and out of mesh ( and, in between, the fork selection mechanism.
Gear Lever Mechanisms
The gear changing mechanism starts, quite obviously, with the gear lever. In early cars the lever ran straight down into the gearbox because the engine and gearbox were separated by a short shaft and this brought the gearbox into a convenient position for a directly-acting lever. The modern practice is to bolt these two major components together, in what became known as "unit construction". This gave greater rigidity to the transmission, as well as cutting manufacturing costs. It did mean, though, that the gearbox was mounted further forward than it used to be and this, in turn, meant that a floor-mounted lever could not be directly coupled to the gearbox. If it was it would have been extremely awkward for the driver, being either too far forward or so long that efficient, accurate changes would be difficult to achieve. The answer was to incorporate a remote control mechanism between the lever and the gearbox. Most floor-mounted, remote control mechanisms are based on a rod, though cables have been used, the rod running forward from the gear lever to the striker arm in the gearbox. This may sound simple enough but there are problems involved in this type of linkage.
Most stem from the fact that a gear lever must move in two planes, forward and back and then from side to side to move across the gear "gate". The connecting rod must obviously be able to duplicate these movements. A rod that is simply bolted to the gear lever and striker arm could move in both directions, but its action would undoubtedly be harsh. Also, the distance between the lever and the striker arm is often around 70 cm (2ft) and a rod of this length must be supported in bearings if it is to transmit the gear lever's movements smoothly and without any flexing. Incorporating plain bearings or bushes would not affect the back and forth movement of a simple rod but they would clearly prohibit side to side action. The answer to the problem is simple. Most remote control rods are cranked at the gear lever end. This means that the sideways action of the lever is converted into rotation of the rod, an action with which the simple bearings do not interfere.
Selector Forks
The job of the gear lever is to move the selector forks, which are those components that actually slide the dog clutches in and out of mesh. The forks, one for each dog clutch, locate in grooves in the dog and are in constant contact. Wear and tear on the forks is minimized by manufacturing them from extremely hard steel. The operation of the forks is very simple. They are carried on rods that run parallel with the gearbox shafts and when a gear change is required the relevant fork is moved along its shaft. Its location in the groove means that the dog clutch is carried with it, bringing it into contact with the pinion to be engaged. Similarly, when this pinion has to be disengaged, the fork simply slides down the rod, carrying the dog clutch away from the pinion.

With the gearbox of the conventional car installed right behind the clutch and the gear lever placed close to the driver, the two must be connected by a remote control rod in the gearbox casing.
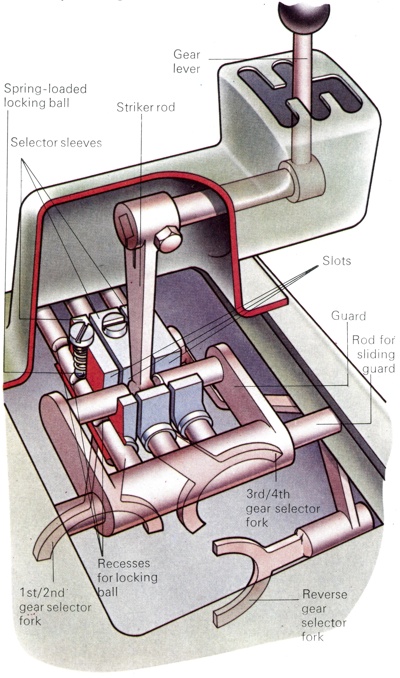
The striker rod of a sliding selector mechanism is guided across the gearbox by the driver and moves the guard to expose the slot in a sleeve. The striker rod enters the slot, and further movement of the gear lever slides the sleeve along its rod to engage a gear. A locking ball engages a recess in the rod to hold the sleeve.
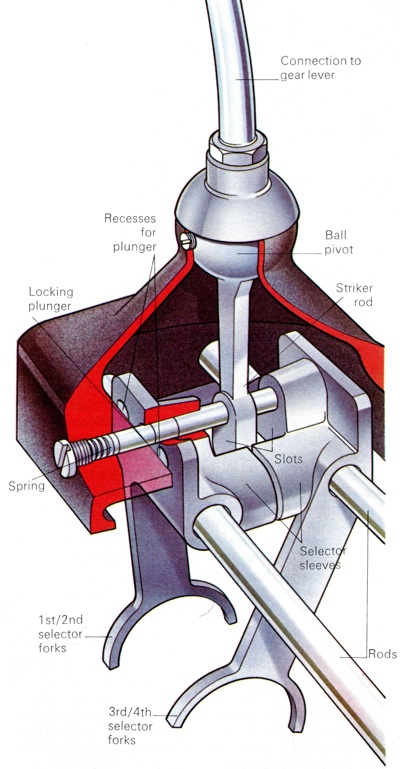
The ball-type selector has a similar striker rod but a different guard, which is part of the locking plunger. When the striker moves sideways it disengages the plunger and engages the selector sleeve's slot. Movement of the plunger also unlocks the selector sleeve, so it is then free to slide along its rod and engage a gear.

The rod of a column-mounted gearchange runs down either the side or centre of the steering column. Two movements, raising the lever and turning the rod, select and engage the gears.

The gearchange used on the Renault 4 ran through the fascia to the gearbox. Twisting the rod selected the gear (via the auxiliary lever) and sliding the rod engaged it. |
Gear Changing
A good many drivers think of gear changing as one simple action. This is more a tribute to the design of gear changing mechanisms than a reality, because a change of gear does, in fact, comprise four separate stages. To take the sequence in turn, the gear lever must first be moved to select the correct fork and is then used to move it in the appropriate direction. Then the dog clutch must be engaged with the pinion and, lastly, the dog must be locked in position. The third of these tasks, that of engaging the dog clutch with the pinion, is really the task of synchromesh but all the others fall firmly in the province of the gear selector mechanism. There are two common gear selector mechanisms that are of concern to the classic car enthusiast, the sliding selector and the ball-type, though these were greatly modified and improved by individual manufacturers.
The Sliding Selector Mechanism
The sliding selector mechanism has four rods and three of them run along the gearbox parallel with the mainshaft, while the fourth rod runs at right angles to them. When this type of mechanism is employed on a four-speed gearbox there are also three selector forks all fitted with sleeves. Two of the forks fit directly on to the longer rods, while the third, for reverse gear, is connected to the sleeve on the other long rod by means of a lever. The sleeves on the forks have two distinct features. First they are slotted and second they are equipped with spring-loaded ball-bearings that locate in recesses on the rods. When the gearbox is in neutral these slots are in line across the gearbox. The fourth rod carries a guard and has a pair of fingers facing each other but with a narrow space between them.
The lower portion of the gear lever, called the striker rod, fits in between these fingers and its tip engages with one of the slots. In this position the fingers of the guard are located in the slots of the forks that are not engaged, therefore the striker rod is prevented from engaging two forks at once. Now, to change to another selector the striker rod clearly has to be moved across the gearbox. This movement is provided by the driver when he moves the lever across the gear gate. On its way across, the striker rod pushes the guard in front of it, thus exposing the slot in the desired fork. The second finger of the guard moves behind the striker rod, closing the slot that the striker rod has just left, again preventing the chance of inadvertently engaging two slots at once.
With the striker rod firmly engaged in the slot the fork can be moved. This takes place when the gear lever is moved either forward or backward. The pressure exerted on the gear lever must be sufficient to overcome the force of the ball-bearing's spring but a firm movement of the gear lever by the driver provides this. Once moving up the shaft, the fork continues its forward travel until the dog clutch contacts the teeth on the side of the gear to be engaged. The synchromesh mechanism then allows the teeth to be moved into full engagement but the dog has still to be locked in position. This is done by the spring-loaded ball in the fork's collar. The rod carrying the fork has another recess at the point reached by the collar when the dog is fully engaged. The spring, therefore, pushes the ball into the recess, effectively locking the fork to the rod and, if the fork cannot move, it will resist any tendency of the dog to disengage itself from the pinion.
Disengagement is the reverse of this process. If the gear to be engaged is operated by the same dog clutch as the one already in use, as would be the case in a change from fourth to third, for example, the driver, by moving the gear lever, forces the sprung ball back into its socket in the fork's collar, the fork moves up the shaft, engages the other pinion and re-locks itself to another slot in the rod. The process is slightly more complex if the gear change is to be made across the gate, from third to second, for example. In this case the fork is slid back into its original position. The lever is then moved sideways by the driver and this movement also forces the striker rod sideways. This action again moves the guard, exposing one fork's slot and closing the one it previously occupied. With the fork selected, the striker lever is then moved either forward or backward, sliding the new dog clutch up the mainshaft splines and locking it in position.
The Ball-Type Selector
Like the sliding selector mechanism described above, the forks in the ball-type selector are each mounted on rods in the upper section of the gearbox. These rods run through the sleeves of the forks, each of which has a deep slot cut in one side to receive the striker rod. The striker rod protrudes down between the fork sleeves, so that any sideways movement will engage the rod in a slot. Moving the gear lever forward or backward will then move the fork along the rod, sliding the dog clutch along the gearbox mainshaft. The sleeves are, however, locked to the rods to prevent accidental engagement of more than one fork sleeve. The locking device that is used centres on a spring-loaded plunger, there being one plunger fitted for each selector fork.
The spring is located in the gearbox housing and it forces a small plunger into a recess in the fork's sleeve. To fully engage the fork, the striker rod must therefore first compress the plunger. The extra movement of the striker rod that this involves takes the striker rod well clear of the other fork, which is, in any case, itself locked by a plunger. When the fork has engaged the dog clutch and pinion it is locked to its rod by the same plunger. The spring forces this away from the gearbox casing and slips it into another recess in the fork's sleeve. Both of these selector mechanisms are relatively complex. They rely on a large number of moving parts and are consequently liable to develop faults, as well as being expensive to manufacture. It is hardly surprising therefore, that makers of less-expensive cars have sought to simplify their selector mechanisms as far as possible. Two examples, the Vauxhall Viva and the Ford Escort, show significant advances in this respect on the systems just described.
The Vauxhall Viva Selector Mechanism
The gear selector mechanism fitted to the Vauxhall Viva HA and HB models and the earlier 4-cylinder Holden Torana models was significantly simpler than those described above. The main feature of this design was that it had only two rods. The first of these was connected directly to the car's gear lever. This rod had three broad teeth projecting from it and the far end, pivoted in the gearbox casing, had a series of grooves. These grooves accepted a spring-loaded ball which effectively locked the rod in position whenever a gear change was made. The rod also passed through a slotted collar which had three large bosses. The second rod was stationary and carried the selector forks for the forward gears. These forks had shoulders that were wide enough to match the space between the teeth on the remote control rod. The shoulders were off-set slightly, however, so that only one could be engaged by the teeth at any time.
When the gearbox was in "Neutral" the line of the remote control lever ran between the shoulders on the selector forks. To engage first gear the driver pushed the gear lever across to the left. As the lever was pivoted, this meant that the remote control rod would turn to the right. The turning movement brought two of the teeth on the remote control rod into mesh with the shoulder on the first/second gear selector fork. The gear lever was then pushed forward by the driver, so the control rod slid backwards. The teeth on the control rod, therefore, pulled the selector fork in the same direction. The slotted collar, which had turned with the control rod, would stay in position, so that its bosses prevented any movement of the other selector fork. The pull on the control rod was sufficient to force back the spring-loaded locking ball, which then located into another of the rod's slots when the gear change was completed.
The change up into second gear was quite straight-forward. The driver simply pulled the gear lever back, thereby forcing the control rod forward. This movement pushed the first/ second gear selector fork back, through the neutral position and it kept moving until the dog clutch engaged the second gear pinion. The next gear change in the sequence, up into third gear, involved slightly more action. First of all the driver returned the gear lever to the neutral position, with the result that the control rod slid back and turned to the left, thus releasing the teeth from the first/second selector fork's shoulder. The driver then pushed the gear lever over to the right, which meant that the control rod would turn still further to the left and bring its other teeth into mesh with the shoulder on the third/fourth gear selector fork. The slotted collar would turn with the rod, thus locating its bosses on either side of the first/second gear fork. Finally the driver pushed the lever forward, sliding the control rod back and drawing the selector fork with it. The sequence of gear changes then followed the pattern already described: the control rod turned when the gear change was to be made across the gate and slid either forward or backward to bring the dogs into and out of engagement.
The Ford Escort Selector Mechanism
The gearbox used in the Ford Escort simplifies the system still further. It used a single rod to both mount the selector forks and to control their movements The selector rod ran from the gear lever right through the top of the gearbox and was pivoted in the wall behind the bell-housing. The bell-housing end of the control rod has three notches and a spring-loaded plunger located in one of these, effectively locking the rod in position but it could slide into any one of three positions when sufficient pressure was exerted via the gear lever. Fixed rigidly to the rod was a boss, with a peg protruding from one side. This peg formed the gear selector arm. Either side of this boss were two selector forks one for third and fourth gears and one for second and first gears.
The selector rod ran through a sleeve in the forks in the usual way. The forks were a loose fit on the rod and were loose enough for the rod to slide through them. Each of these forks had a narrow tongue that was integral with the sleeve. The tongues ran parallel with the selector rod and each had a slot cut into the side nearest the rod. The selector for reverse gear was pivoted on a pin in the wall of the gearbox case. It, too, had a slotted tongue and this ran up towards the selector rod. The selector tongues met in a "stack" but there was a small clearance between each. The tongue from the third/fourth selector was uppermost, the first/second selector tongue was in the middle and the tongue from the reverse selector was at the bottom.
Finally, pivoted on one side of the gearbox case was a locking plate. This was bored to allow the selector rod to pass through it with a generous clearance. One edge of this bore was pierced to form a pair of teeth. The crucial parts of the selector mechanism were the stack of selector tongues, the peg on the selector arm and the locking plate. When the gearbox was in neutral the peg on the selector arm was between the tongues of the third/fourth and first/ second selectors. Now, when the driver wanted to engage first gear they moved the gear lever to their left. This would cause the main selector rod to turn to the left as well and this was a downward movement. This would lower the selector peg into the slot on the first/second gear selector tongue. The driver then moved the gear lever forward to engage the gear. Being pivoted, this would cause the lever to draw the selector rod backwards and, as the peg was located in the slot, the rod would draw the selector with it, thereby bringing the dog clutches into engagement.
The other selectors were prevented from moving by the locking plate. When the peg engaged the first/second selector the teeth of the locking plate were in the slots of the other selectors. The locking plate, therefore, resisted any tendency of the other selectors to move with the rod. When the first gear dog clutch was engaged with its pinion the selector rod would have moved by the distance of one of the notches at the bell-housing end. The spring-loaded plunger would, therefore, slip into the new notch, locking the selector rod in that position. The change into second gear was fairly straight-forward. The gear lever was simply pulled back by the driver, which resulted in a forward movement of the selector rod. The pressure on the rod forced back the spring plunger and the rod carried the selector back, through the neutral position and into engagement with the second gear pinion.
The change into third was more complex, however, because the mechanism had to travel across the gate. To change into third gear the driver pushed the lever back and moved it into neutral. They then moved the lever across to the right. This movement to the right resulted in the selector rod rising. The peg on the selector arm, therefore, entered the slot in the third/fourth selector fork. To complete the gear change the driver then pushed the lever forward and the selector rod consequently moved backward, taking the fork with it. The initial movement of the peg pushed the locking plate out of the third/fourth selector slot. This movement would, however, raise the locking plate's lower tooth into the slots in the other selector tongues, thereby ensuring that they remained in position during the time that the gear change took place. The rest of the gear changes followed this sequence. The peg turned to select its fork and controlled the locking plate as it did so. The selector rod then moved forward or backward to bring the dog clutch and pinion into engagement. Once disengaged, the selector returned to its original position.
Steering Column Mounted Gear Levers
Steering column-mounted gear levers were most widely used in the UK by Ford and Vauxhall, both American-owned companies. The fashion for this type of linkage reached its peak in Britain in the late 1950's and early 1960's and was an almost direct reflection of the American trend. Here in Australia it was widely used by the big three -
Holden, Ford and
Chrysler. The "Three-On-The-Tree" main advantages were the styling innovations that it allowed. With a steering column gear lever a bench seat could be fitted.
A steering column gear change does, however, possess rather more significant disadvantages. The linkage to the gearbox is complex, involving a series of rods and swivels. These are relatively costly to manufacture and require accurate adjustment if a reliable gear change is to be achieved. Lubrication of the linkage is a further problem, being a point that is easily overlooked in servicing, though GM did develop a system whereby certain key joints were automatically lubricated by oil from the gearbox itself. Though the selector mechanism of a steering column gear change is often essentially the same as those outlined above, the linkage to the gearbox is radically different.
Where most floor-mounted gear change mechanisms rely on a remote control shaft, steering column gear changes use a rod running to either the middle or the side of the steering column itself. The gear change lever is pivoted to the top of this rod. A bracket which provides the fulcrum for the gear lever is also connected to the rod and can turn with it. To change gear the driver moves the lever across the gate which means either pulling the lever towards them or pushing it away from them. This movement turns the rod in the bushes that support it and selects the gear to be changed. The driver then lifts the lever clockwise or anti-clockwise and this results in the rod either moving down or up respectively. These movements are used to actually move the selector forks into position and to change the gears.
Fascia-Mounted Gear Changes
A gear change mechanism mounted on the fascia is relatively rare, though they were used extensively in the Renault range and on some Citroen models. Their use was due largely to mechanical rather than styling considerations. The models in which they were used were mostly equipped with front-wheel drive transmissions that had the gearbox placed in front of the engine. This meant that a conventional floor-mounted gear lever would need a very complex linkage to reach the selector mechanism in the gearbox itself. At first sight this gear changing mechanism seems very difficult to operate, the driver must push, pull and turn the gear control rod in an initially confusing manner. But this type of control is, in fact, relatively simple.
The gear lever or "knob" is simply attached to a shaft that runs right through the fascia and over the engine to the gearbox. It connects to an auxiliary lever that is directly coupled to the selector mechanism. The shaft is supported by a series of bushes or bearings. To operate the gears the driver turns the knob to the left or to the right, causing the shaft to rotate in its bushes and to move the auxiliary lever laterally. This movement selects the appropriate fork. The driver then pulls the knob towards / or pushes it away, which slides the selector and makes the gear change.
Cable gear mechanisms
Cables provide another means of connecting the gear lever to the selector mechanism. Like the fascia-mounted system described above, a cable linkage can be useful in making the connection to an awkwardly placed gearbox. It has the advantage of being cheap to manufacture but unfortunately it also has serious drawbacks. The worst of these was well demonstrated by the British Leyland Maxi. Launched in
1969, the Maxi's gear change was an immediate target for criticism as it was extremely stiff and awkward to operate. At that stage the Maxi was fitted with a cable gear change and the problem was traced to the long-known fact that while a cable can pull very effectively it is far less efficient when a pushing effort is required. This basic trouble was exacerbated by the fact that a heavy pocket of grease accumulated at the point where the Maxi's cables entered the gearbox housing. The cables therefore had to force their way through this grease in order to operate and the extra effort required resulted in the stiff gear lever action.
The problem was solved within a year of the car's launch when the gear linkage was re-designed to operate on a rod system. The reverse problem is true of most cable gear changes, which acquired a reputation for being sloppy and imprecise. It may be true that a cable gear change cannot achieve quite the precision of one that is directly connected to the gearbox, but really bad examples of a loose change are more likely to be the result of neglected maintenance rather than poor original design. Adjustment of a cable gear change is usually a painstaking operation, but it can make driving a good deal easier. The general problem of a cable being inefficient as a means of applying a pushing load was overcome in a variety of other ways. Some manufacturers used extremely heavy cables that were less liable to buckle under compression, while others went further and encased the cables in tubing. The final problem peculiar to cable linkages was the fact that after long periods of use the cables tended to stretch, which threw the entire linkage out of adjustment and the cables then had to be adjusted or replaced.